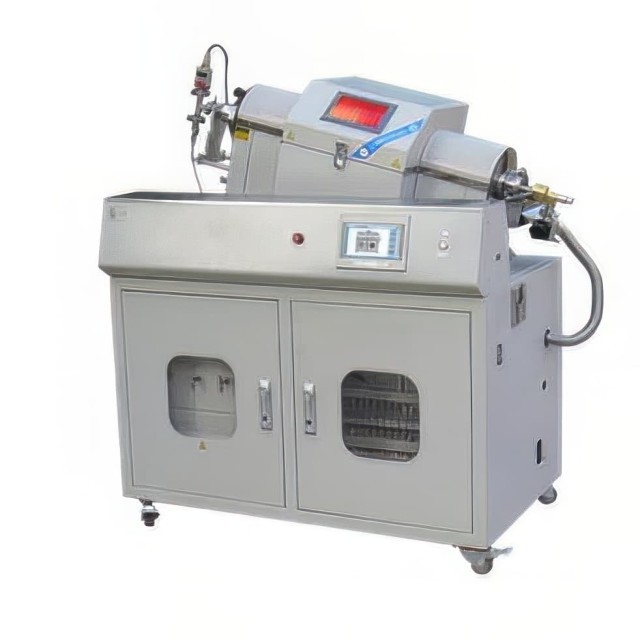
CVD & PECVD Furnace
Inclined Rotary Plasma Enhanced Chemical Deposition PECVD Tube Furnace Machine
Item Number : KT-PE16
Price varies based on specs and customizations
- Max. temperature
- 1600℃
- RF Plasma Output Power
- 5 -500W adjustable with ± 1% stability
- Rated vacuum pressure
- 10Pa (Standard), 6x10-5Pa (High vacuum optional)
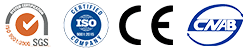
Shipping:
Contact us to get shipping details Enjoy On-time Dispatch Guarantee.
Why Choose Us
Reliable PartnerEasy ordering process, quality products, and dedicated support for your business success.
Inclined Rotary Plasma Enhanced Chemical Deposition (PECVD) Tube Furnace
The Inclined Rotary Plasma Enhanced Chemical Deposition (PECVD) Tube Furnace Machine is a sophisticated system designed for advanced materials research and production. It utilizes a rotating furnace tube and a plasma generator to induce chemical reactions in a gaseous discharge, enabling the formation of high-quality solid deposits on various materials. This precise control over the deposition process makes it invaluable for cutting-edge applications.
Key Features & Benefits for Your Research
Our PECVD Tube Furnace is engineered to deliver precision, efficiency, and versatility to your laboratory:
- Enhanced Deposition Quality:
- Uniform Mixing and Heating: The rotating furnace tube, featuring a variable-diameter design and mixing baffle, ensures thorough material mixing and consistent temperature distribution, leading to uniform and high-quality depositions.
- Versatile Plasma Source: The RF plasma source (5-500W, automatic matching) provides stable and adjustable power, increasing activation energy, lowering reaction temperatures, and improving overall process efficiency for tailored material deposition.
- Precise Process Control:
- Accurate Temperature Management: PID programmable temperature control offers exceptional accuracy (±1℃) and stability, allowing for precise heating and cooling cycles crucial for achieving optimal material properties. Supports remote and centralized control.
- Controlled Gas Environment: High-precision MFC mass flowmeters (up to 4 channels) and a gas mixing device enable precise control over gas composition and flow rates, vital for optimizing deposition processes for specific materials and applications.
- Efficient Vacuum System: Equipped with a high-performance mechanical pump for rapid evacuation of the furnace tube to vacuum. Optional high vacuum units (e.g., up to 6x10-5Pa with molecular pump) are available for demanding processes.
- User-Friendly Operation & Durability:
- Intuitive Interface: The CTF Pro controller with a 7-inch TFT touch screen allows for user-friendly program setting, real-time data monitoring, historical data analysis, and remote control capabilities, streamlining operations.
- Rapid Processing: An automated furnace chamber sliding system facilitates quick heating and cooling, minimizing processing time and enhancing productivity. Auxiliary fast cooling and automatic sliding movement are available.
- Robust Construction: Built with a stainless steel vacuum flange with adaptable ports, ensuring reliable sealing and high vacuum levels for a pristine deposition environment. Designed for top performance, low maintenance, easy installation, and a long working life.
Technical specifications
Furnace model | PE-1600-60 |
---|---|
Max. temperature | 1600℃ |
Constant work temperature | 1550℃ |
Furnace tube material | High purity Al2O3 tube |
Furnace tube diameter | 60mm |
Heating zone length | 2x300mm |
Chamber material | Japan alumina fiber |
Heating element | Molybdenum Disilicide |
Heating rate | 0-10℃/min |
Thermal couple | B type |
Temperature controller | Digital PID controller/Touch screen PID controller |
Temperature control accuracy | ±1℃ |
RF Plasma unit | |
Output Power | 5 -500W adjustable with ± 1% stability |
RF frequency | 13.56 MHz ±0.005% stability |
Reflection Power | 350W max. |
Matching | Automatic |
Noise | <50 dB |
Cooling | Air cooling. |
Gas precise control unit | |
Flow meter | MFC mass flow meter |
Gas channels | 4 channels |
Flow rate | MFC1: 0-5SCCM O2 MFC2: 0-20SCMCH4 MFC3: 0- 100SCCM H2 MFC4: 0-500 SCCM N2 |
Linearity | ±0.5% F.S. |
Repeatability | ±0.2% F.S. |
Pipe line and valve | Stainless steel |
Maximum Operating Pressure | 0.45MPa |
Flow meter controller | Digital Knob controller/Touch screen controller |
Standard vacuum unit(Optional) | |
Vacuum pump | Rotary vane vacuum pump |
Pump flow rate | 4L/S |
Vacuum suction port | KF25 |
Vacuum gauge | Pirani/Resistance silicon vacuum gauge |
Rated vacuum pressure | 10Pa |
High vacuum unit(Optional) | |
Vacuum pump | Rotary vane pump+Molecular pump |
Pump flow rate | 4L/S+110L/S |
Vacuum suction port | KF25 |
Vacuum gauge | Compound vacuum gauge |
Rated vacuum pressure | 6x10-5Pa |
Above specifications and setups can be customized |
Applications
The precision and versatility of our PECVD Tube Furnace make it ideal for a wide range of applications, empowering innovation in fields such as:
- Semiconductor Manufacturing: Deposition of thin films like silicon nitride, silicon dioxide, and polysilicon on wafers.
- Solar Cell Production: Creation of thin films such as cadmium telluride and copper indium gallium selenide.
- Flat Panel Display Technology: Deposition of materials like indium tin oxide and zinc oxide.
- Optical Coatings: Application of thin films like titanium dioxide and silicon nitride on optical components.
- Medical Device Manufacturing: Coating medical devices with biocompatible or functional thin films such as hydroxyapatite and titanium nitride.
Operating Principle
The Inclined Rotary Plasma Enhanced Chemical Deposition (PECVD) Tube Furnace Machine operates as a plasma-enhanced rotary chemical vapor deposition system. Its furnace tube adopts a variable-diameter design with a mixing baffle, allowing for uniform heating and efficient mixing of materials. An inductively coupled plasma generator covers the furnace tube, providing increased activation energy, which can lower reaction temperatures and improve efficiency. The equipment utilizes a three-way mass flow meter and gas mixing device for precise gas control. Additionally, a high-performance mechanical pump enables rapid evacuation of the furnace tube, creating a vacuum environment suitable for various CVD processes.
Safety Features
Safety is paramount in our design. The KINTEK tube furnace incorporates multiple safety mechanisms:
- Over-current protection and over-temperature alarm functions, which automatically shut off power if limits are exceeded.
- Built-in thermocouple break detection; the furnace will stop heating and trigger an alarm if a failure is detected.
- The PE Pro controller supports a power failure restarting function, allowing the furnace to resume its heating program once power is restored.
Standard Package
No. | Description | Quantity |
---|---|---|
1 | Furnace | 1 |
2 | Quartz tube | 1 |
3 | Vacuum flange | 2 |
4 | Tube thermal block | 2 |
5 | Tube thermal block hook | 1 |
6 | Heat resistant glove | 1 |
7 | RF plasma source | 1 |
8 | Precise gas control | 1 |
9 | Vacuum unit | 1 |
10 | Operation manual | 1 |
Optional Setups & Customization
Tailor the PECVD system to your specific research needs with our range of optional setups:
- In-tube gas detection and monitoring (e.g., H2, O2).
- Independent furnace temperature monitoring and recording.
- RS 485 communication port for PC remote control and data exporting.
- Control of insert gas feeding flow rates (e.g., mass flowmeter and float flowmeter).
- Advanced touch screen temperature controller with versatile, operator-friendly functions.
- High vacuum pump station configurations (e.g., vane vacuum pump, molecular pump, diffusion pump).
Your Partner in Advanced Material Science
Leveraging exceptional R&D and in-house manufacturing, KINTEK provides diverse laboratories with advanced high-temperature furnace solutions. Our product line, including Muffle, Tube, Rotary Furnaces, Vacuum & Atmosphere Furnaces, and CVD/PECVD/MPCVD Systems, is complemented by our strong deep customization capability to precisely meet your unique experimental requirements.
Ready to elevate your research with our Inclined Rotary PECVD Tube Furnace? Our experts are available to discuss your specific application, explore customization options, or provide a detailed quotation. Contact us today to learn more!
FAQ
What Are The Main Applications Of A Rotary Tube Furnace?
What Is A Tube Furnace And How Does It Work?
What Is The Principle Of A Rotary Furnace?
What Is A PECVD Machine Used For?
What Is A Rotating Furnace Used For?
What Is The Principle Of A CVD Machine?
What Is The Principle Of An MPCVD Machine?
What Are The Main Applications Of Multi-zone Tube Furnaces?
What Are The Key Features Of A Rotary Tube Furnace?
What Are The Main Applications Of Tube Furnaces?
What Are The Advantages Of Using A Rotary Furnace?
What Are The Main Types Of PECVD Machines?
What Are The Main Types Of Rotating Furnaces Available?
What Are The Advantages Of Using A CVD Machine?
What Are The Advantages Of Using An MPCVD Machine?
What Are The Key Features Of Multi-zone Tube Furnaces?
How Does A Rotary Tube Furnace Work?
What Are The Advantages Of Using A Tube Furnace?
What Are The Key Features Of A Rotary Furnace?
How Does A PECVD Machine Work?
How Does A Rotating Furnace Work?
What Are The Applications Of A CVD Machine?
What Are The Key Applications Of MPCVD Machines?
How Does A Multi-zone Tube Furnace Work?
What Are The Advantages Of Using A Rotary Tube Furnace?
What Types Of Tube Furnaces Are Available?
What Are The Common Applications Of A Rotary Furnace?
What Are The Key Features Of A PECVD Machine?
What Are The Advantages Of Using A Rotating Furnace?
What Are The Key Features Of A CVD Machine?
What Are The Main Components Of An MPCVD Machine?
What Are The Advantages Of Using A Multi-zone Tube Furnace?
What Temperature Can A Rotary Tube Furnace Reach?
What Temperature Ranges Can Tube Furnaces Achieve?
How Does A Rotary Furnace Handle Different Materials?
What Are The Advantages Of Using A PECVD Machine?
What Safety Features Are Included In Rotating Furnaces?
What Types Of CVD Machines Are Available?
How Does An MPCVD Machine Enhance Energy Efficiency?
What Types Of Multi-zone Tube Furnaces Are Available?
What Types Of Materials Can Be Processed In A Rotary Tube Furnace?
Can Tube Furnaces Operate Under Different Atmospheres?
What Materials Can Be Deposited Using A PECVD Machine?
Can Rotating Furnaces Be Customized For Specific Applications?
Why Is MPCVD Preferred For Diamond Growth?
What Makes KINTEK Tube Furnaces Special?
Why Is PECVD Preferred Over Other Deposition Methods?
4.8
out of
5
This machine is a game-changer! The plasma enhancement works flawlessly, and the inclined rotary design is brilliant.
4.7
out of
5
Incredible value for money. The quality is top-notch, and it arrived faster than expected. Highly recommend!
4.9
out of
5
The durability is impressive. We've used it daily for months with zero issues. A solid investment!
4.8
out of
5
Cutting-edge technology at its finest. The PECVD process is so efficient, it’s like magic!
4.7
out of
5
Superb delivery speed and setup was a breeze. The machine performs beyond expectations.
4.9
out of
5
The precision and consistency are unmatched. This is what technological advancement looks like!
4.8
out of
5
Worth every penny! The build quality is exceptional, and it’s incredibly user-friendly.
4.7
out of
5
Fast delivery and outstanding performance. This machine has revolutionized our lab’s workflow.
Products
Inclined Rotary Plasma Enhanced Chemical Deposition PECVD Tube Furnace Machine
REQUEST A QUOTE
Our professional team will reply to you within one business day. Please feel free to contact us!
Related Products
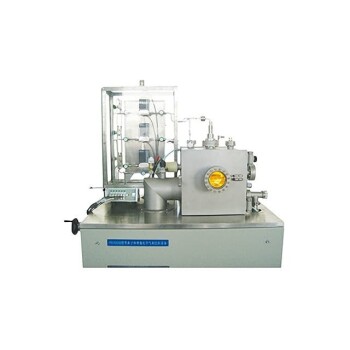
Inclined Rotary Plasma Enhanced Chemical Deposition PECVD Tube Furnace Machine
KINTEK's PECVD coating machine delivers precision thin films at low temperatures for LEDs, solar cells & MEMS. Customizable, high-performance solutions.
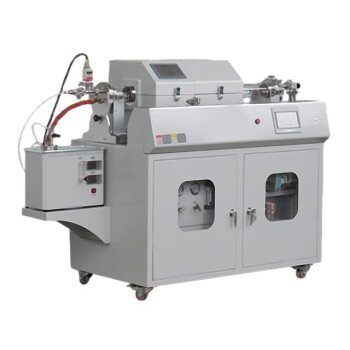
Slide PECVD Tube Furnace with Liquid Gasifier PECVD Machine
KINTEK Slide PECVD Tube Furnace: Precision thin film deposition with RF plasma, rapid thermal cycling, and customizable gas control. Ideal for semiconductors and solar cells.
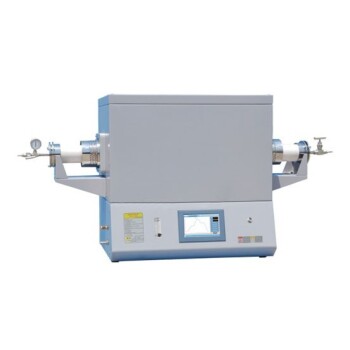
1700℃ High Temperature Laboratory Tube Furnace with Quartz or Alumina Tube
KINTEK's Tube Furnace with Alumina Tube: Precision heating up to 1700°C for material synthesis, CVD, and sintering. Compact, customizable, and vacuum-ready. Explore now!
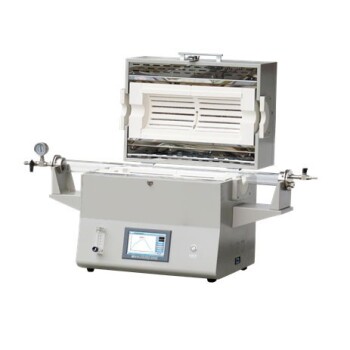
1400℃ High Temperature Laboratory Tube Furnace with Quartz and Alumina Tube
KINTEK's Tube Furnace with Alumina Tube: Precision high-temperature processing up to 2000°C for labs. Ideal for material synthesis, CVD, and sintering. Customizable options available.
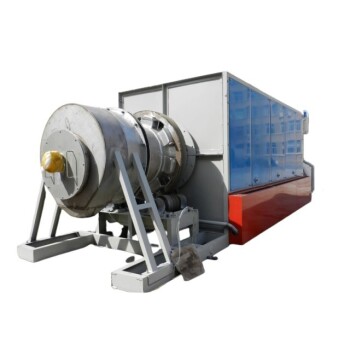
Electric Rotary Kiln Small Rotary Furnace for Activated Carbon Regeneration
Electric Activated Carbon Regeneration Furnace by KINTEK: High-efficiency, automated rotary kiln for sustainable carbon recovery. Minimize waste, maximize savings. Get a quote!
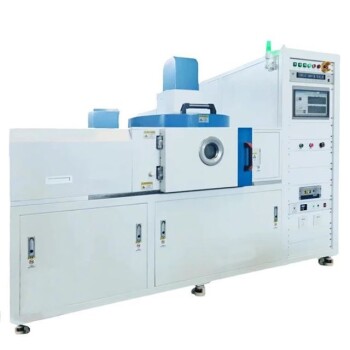
RF PECVD System Radio Frequency Plasma Enhanced Chemical Vapor Deposition
KINTEK RF PECVD System: Precision thin-film deposition for semiconductors, optics & MEMS. Automated, low-temperature process with superior film quality. Custom solutions available.
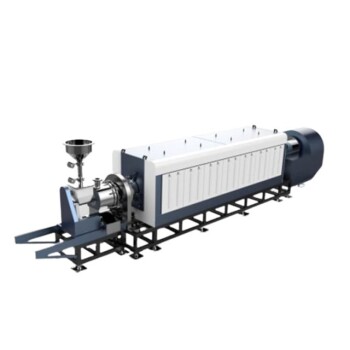
Electric Rotary Kiln Small Rotary Furnace Biomass Pyrolysis Plant Rotating Furnace
KINTEK's Rotary Biomass Pyrolysis Furnace converts biomass to biochar, bio-oil, and syngas efficiently. Customizable for research or production. Get your solution now!
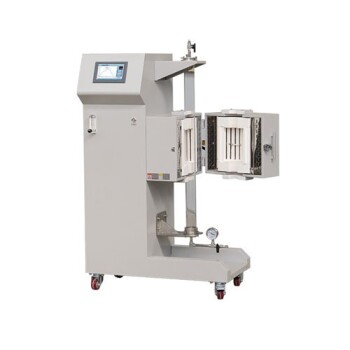
Vertical Laboratory Quartz Tube Furnace Tubular Furnace
Precision KINTEK Vertical Tube Furnace: 1800℃ heating, PID control, customizable for labs. Ideal for CVD, crystal growth & materials testing.
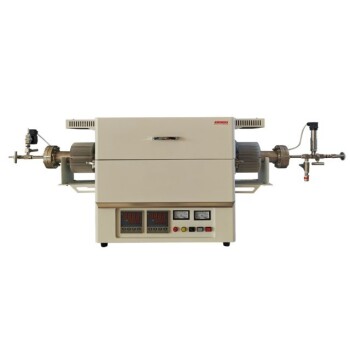
High Pressure Laboratory Vacuum Tube Furnace Quartz Tubular Furnace
KINTEK High Pressure Tube Furnace: Precision heating up to 1100°C with 15Mpa pressure control. Ideal for sintering, crystal growth, and lab research. Customizable solutions available.
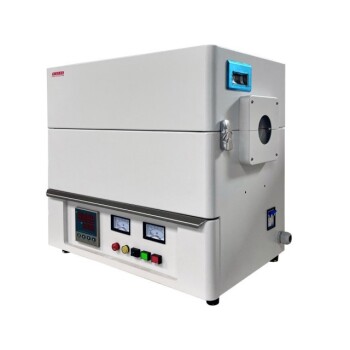
1200℃ Split Tube Furnace Laboratory Quartz Tube Furnace with Quartz Tube
Discover KINTEK's 1200℃ Split Tube Furnace with quartz tube for precise high-temperature lab applications. Customizable, durable, and efficient. Get yours now!
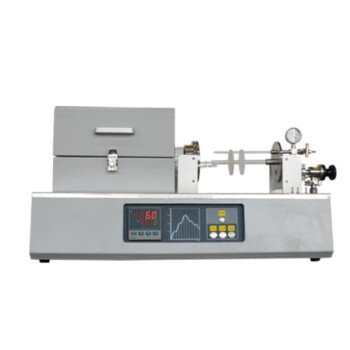
Laboratory Quartz Tube Furnace RTP Heating Tubular Furnace
KINTEK's RTP Rapid Heating Tube Furnace delivers precise temperature control, rapid heating up to 100°C/sec, and versatile atmosphere options for advanced lab applications.
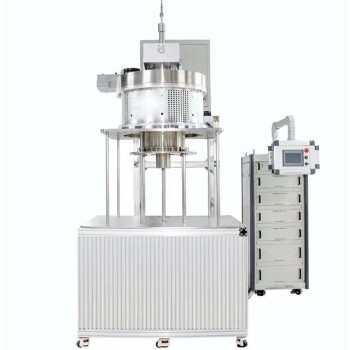
915MHz MPCVD Diamond Machine Microwave Plasma Chemical Vapor Deposition System Reactor
KINTEK MPCVD Diamond Machine: High-quality diamond synthesis with advanced MPCVD technology. Faster growth, superior purity, customizable options. Boost production now!
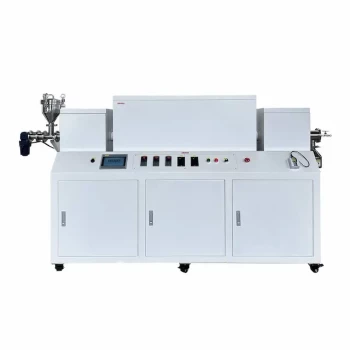
Vacuum Sealed Continuous Working Rotary Tube Furnace Rotating Tube Furnace
Precision rotary tube furnace for continuous vacuum processing. Ideal for calcination, sintering, and heat treatment. Customizable up to 1600℃.
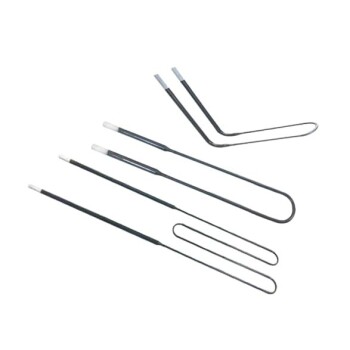
Molybdenum Disilicide MoSi2 Thermal Heating Elements for Electric Furnace
High-performance MoSi2 heating elements for labs, reaching 1800°C with superior oxidation resistance. Customizable, durable, and reliable for high-temperature applications.

Multi Heating Zones CVD Tube Furnace Machine for Chemical Vapor Deposition Equipment
KINTEK's Multi-Zone CVD Tube Furnaces offer precision temperature control for advanced thin film deposition. Ideal for research and production, customizable for your lab needs.
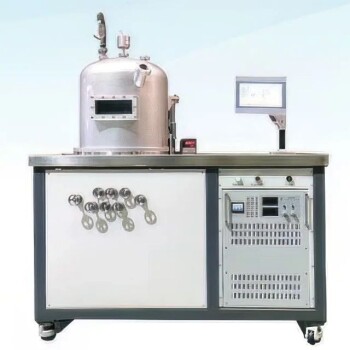
HFCVD Machine System Equipment for Drawing Die Nano Diamond Coating
KINTEK's HFCVD system delivers high-quality nano-diamond coatings for wire drawing dies, enhancing durability with superior hardness and wear resistance. Explore precision solutions now!
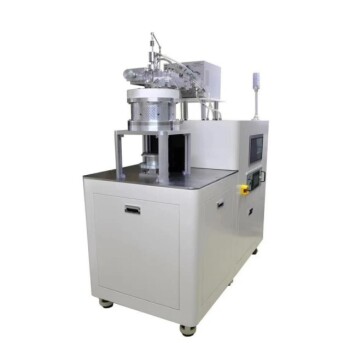
MPCVD Machine System Reactor Bell-jar Resonator for Lab and Diamond Growth
KINTEK MPCVD Systems: Precision diamond growth machines for high-purity lab-grown diamonds. Reliable, efficient, and customizable for research and industry.
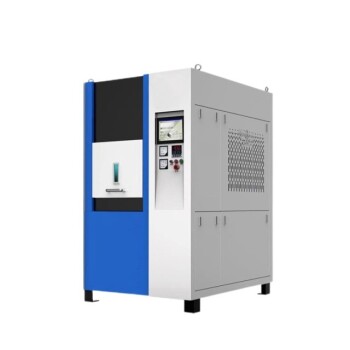
Spark Plasma Sintering SPS Furnace
Discover KINTEK's advanced Spark Plasma Sintering (SPS) Furnace for rapid, precise material processing. Customizable solutions for research and production.
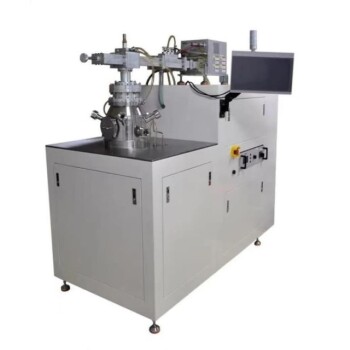
Cylindrical Resonator MPCVD Machine System for Lab Diamond Growth
KINTEK MPCVD Systems: Grow high-quality diamond films with precision. Reliable, energy-efficient, and beginner-friendly. Expert support available.